What happens when you return bottles in Michigan?
Expert weighs in on the logistics behind state’s deposit program
Michigan’s dime deposit program is almost 50 years old and is always in the news because of efforts to expand or repeal it. But, do you know what happens to that plastic and aluminum when you take it back to a retailer?
Frederick Lawrence is a logistics faculty in CMU’s College of Business Administration and is the director of internships for the logistics management program. He answers questions about what happens behind the scenes.
Q. What do retailers do with bottles and cans after people return them?
Retailers take action based on their size, resources and capabilities. Generally, retailers collect cans, separate them by brand and store them in anticipation of pickup by distributors or third-party recyclers.
Larger retailers, like supercenters, commonly have reverse vending machines (RVMs) which allow customers to manually return their own cans. These machines are equipped with conveyors and scanners which detect what cans or bottles are being fed into the machine, if they are accepted by the retailer, and which brand the item is. Once this information is processed, the bottle or can is crushed by a compactor and sorted automatically.
Smaller retailers commonly store cans and bottles in bins or bags in a storage area and the retailer manually separates the containers according to the respective brand.
Q. How does storing those bottles and cans affect the layout of a store?
The storage of cans and bottles can impact store layout, but more accurately, how space is utilized. These effects vary based on store size, resources and typical volume of returns.
Large-scale retailers typically have a dedicated return area, often near an entrance or side of the store, with multiple RVMs to accept consumer returns. Stores design return areas with proper drainage, ventilation and easy-to-clean surfaces to manage spills and odors as manual can-return can be quite messy.
Large-scale retailers also coordinate frequent pickups with distributors or third-party recyclers to avoid recycling overflow and must allocate loading dock space for bottle and can removal. Smaller retailers, because of a lack of automation, face more spatial constraints and often adjust their layout, either by reducing product stock space or by limiting return volumes per customer (retailers in Michigan may limit refunds to $25 per person per day).
Returns can be stored in a variety of locations, including backrooms, basements, behind the checkout counter or even outdoor sheds. This is largely due to the space constraint of being smaller and not having an abundance of extra space available in the layout.
Since small stores typically lack automated compactors, they must store full-size bottles and cans, which take up more space than crushed cans and bottles. This may result in smaller retailers making tradeoffs in how they utilize space; as an extreme example, space that could be used to sell merchandise may have to be retrofitted to store returnable items.
Q. What kind of infrastructure is necessary to transport those bottles and cans?
Transporting returned bottles and cans in Michigan requires a specialized infrastructure that includes collection systems, storage facilities, transportation vehicles and processing centers.
Retailers play an integral role in the collection and storage of claimed returnables (cans and bottles that consumers return themselves). Following this, cans and bottles are picked up by distributors (like Pepsi or Coca-Cola) and third-party recyclers.
The transportation equipment varies, but can generally involve the use of box trucks, semi-trucks using specialized trailers with compartments for specific recycled materials or compactor trucks (which can be used to crush aluminum in plastic if the retailer has not already done this).
As cost control and value reclamation in this process are critical, haulers generally work to optimize their networks by developing designated collection routes based on retailer locations and return volume. This is called “network optimization” and is one of the many Logistics Management and Supply Chain skills/strategies that Logistics Management majors at CMU learn!
Cans/bottles are crushed and sorted, if they have not been already, and are transported to various processing facilities that can repurpose or reuse the materials.
Q. How much does transporting bottles and cans cost annually?
Exact cost figures are difficult to accurately calculate due to the number of stakeholders and partners involved in recycling bottles and cans and the various methods and resources used (including collection, sorting and transportation expenses). Additionally, not all cost figures associated with these processes are publicly disclosed.
According to Michigan.gov (2025), Michigan's refund rate was approximately 73% in 2023 with total Michigan deposits of $389.5 million and total refunds of $284.6 million. This means that 27%, or approximately $105.3 million of deposits went unclaimed. An unclaimed can or bottle refers to a beverage container for which a deposit was paid at the time of purchase (by the consumer) but was never returned for a refund.
In Michigan, consumers pay a $0.10 deposit per container when purchasing certain beverages. To get this deposit back, individuals must return the empty container to a participating retailer or redemption center. The unclaimed deposit amount is simply the difference between the deposits collected and the deposits refunded statewide.
Of the statewide revenue generated by unclaimed deposits, the funds are divided so that 75% of the revenue goes to the state (used for environmental cleanup and pollution prevention) and 25% goes to retailers (to help cover the general costs of managing returns). Based on 2023 data on unclaimed deposits, the state received about $79 million, and retailers got around $26 million to help offset handling costs associated with returns.
At the statewide level, this process relies on financial tracking rather than container counting, so the state doesn’t need to locate unclaimed containers. In fact, many unclaimed cans and bottles may end up in landfills, as roadside litter, curbside recycling or even hoarded in garages.
Q. What ultimately happens to bottles and cans that are returned to stores?
Ultimately, once bottles and cans are returned to Michigan retailers and are picked up and transported by various distributors and recyclers, the material will be processed.
Aluminum cans are crushed, shredded, and melted down and the molten aluminum is rolled into sheets and used to manufacture new beverage cans. Interestingly, aluminum cans can be recycled and reused relatively quickly, with some recycled aluminum being returned to shelves as new products in as little as 60 days.
Plastic bottles may be washed for reuse, shredded into small flakes or melted. The recycled plastic can be used to create new beverage bottles or even repurposed in clothing (e.g., fleece jackets), carpeting, auto parts and many other plastic goods.
Overall, the goal is to reclaim value in the recycled goods and to reduce the creation and use of new “virgin” plastics. Michigan’s bottle return system works to ensure that a significant percentage of beverage containers are recycled and repurposed rather than ending up in landfills.
About Frederick Lawrence
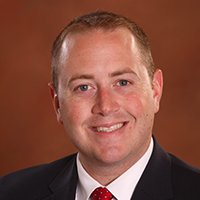